Did you buy a laser machine and you do not know what settings to use on a certain material? These are often times frustrating and most of the laser machine manufacturer had given you the basic guidelines or documents to follow at least to have a baseline of the settings but the truth more often the settings does not work at all on the material that you are using.
The settings that the manufacturer recommend was commonly affected by some factors below:
A. Material Composition – Example : wood – These are commonly what type of wood and How much dryness or water content does it have. Laminated wood such as cherry, pine, cedar, fir, maple, walnut, bamboo etc., are also variable and these are commonly are engineered wood and mainly depends on the manufacturer of the laminated wood: How much glue or ingredients that are present on it when it was laminated, Metal – Stainless – Some Variety of Types , 304,316,310,410 and 420, these types have different content of metal like nickel, carbon, chromium etc. to form an alloy. When Engraving with Thermark, Cermark or Fiber laser, These material also reacts differently and yields on change in color intensity of the engraving even when using the same parameter for all types.
B. Machine Calibration – We know that laser manufacturer was keeping this parameters consistent as possible, but as the years goes by, these parameters depreciates mechanically and commonly the laser source or the tube itself depreciates its power affecting the settings set by the manufacturer and eventually not working anymore. Laser Beam misalignment is also a common factor that the machine settings does not work well as the laser beam spreads or refract on a certain area.
C. Machine Optics Cleanliness – Commonly in a new machine everything works well as the optics are in the manufacturing standard. But as soon as the machine becomes a working horse, It started to build up
dirt on the lenses of the machine. This has to be clean as how you take care of your contact lenses. For you to know how many mirrors that you have to clean is to know where is the outlet of the laser source and look for how many bends does the laser does have in order to bring it up to the table of the machine. In every 90 degree bending there is one mirror. The challenge with engraving using the laser is to keep it clean all the times while it is producing a lot of dust coming from the engraved material.
D. Laser Compensation – Do you realized that as soon as you are processing a dense area of engraving gives you a different result on the loose area engraving. You’ll commonly notice this on a small text and a big text engraving at the same time using the same power, speed, PPI in settings. Most machine has some compensation for this to make it look like almost on the same engraving but some cheap engraving machine most of the time does not have this feature and this affects the settings default given by the manufacturer.
There are certain techniques in finding a setting for your laser settings. If you follow the steps you will not go wrong.
Before we start with the tip Make sure you comply with B and C are corrected and performed.
- Assume you do know the settings for a Certain Material
- Fix one parameter of the Materials settings , for me I normally fix the speed or velocity of the engraving and target the higher speed( I normally set it to 80%: This will help you optimized your setting according to the manufacturability.
- Fixed the Pulse per inch (some use DPI etc.)
- If your machine is capable of running on different color then assign each color a power of = 100,90,80,70,60,50,40,30,20,10
- Create a small square in Corel, AI or other program that your laser uses, ex. o.25″x0.25″ filled by color accordingly base on the assigned power.
- Run the engraving and check for the result.
- With the result, you will know what parameter had engrave too much and the parameter is very good and the parameter that does not engrave anymore.
- Choose the parameter that is in the middle and soo good on the quality. Now change the assigned power and omit all that does too much and not engraving and make it divisible by 2’s instead of 10′ power of ex. p=80,70,60 works well then choose 70 as the middle. Increment and decrement the power by 2’s. ex.P= 80 78, 76,74,72,70 68,66,64, 62, 60.
- repeat until you will get the resolution that you needed and choose the best settings based on the quality of the engraving.
- You always choose the median so you have some room to have some variability on the material and other aspects.
To follow note: will add some pictures for you to follow what I mean on the procedure.
-Lasermoments
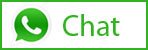
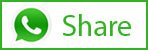